Cutter usage management for rubberwood furniture part machining process
Somchai Puajindanetr, Somnoek Wisuttipaet, and Dusit Thammasang
pp. 361 - 374
Abstract
The objective of this research work was to improve cutter usage management of a vertical-shaft cutting machine for rubberwood furniture industry. The milling cutter used consists of six-straight teeth mounted on the vertical-shaft of a milling machine. A pre-cut rubberwood specimen had the height of 40 mm and outer curve length of 330 mm. The steps of study were (1) studying the current cutter usage management of a factory through studying the important factors of current manually cutting such as specimen feed, cut depth, and cutting speed. (2) Developing the process for improvement of cutter usage management via studying sanding time and roughness after sanding with the coarse and fine size grits of sand paper number 100 and 180, respectively which the furniture factories normally apply; setting-up the surface roughness requirement for a cut-part application; studying a suitable cutting condition for part machining by controlling the cutting factors, and also determining the tool life that provided the cut-surface roughness equivalent to the roughness sanded by the sand paper number 100; and finally, developing the method for improvement.
The study found that (1) the specimen feed had a significant effect on tool life. The higher feed caused a decreased tool life and an increased cut surface roughness; (2) the cutter was used to cut the specimen until the cut surface of specimen was torn grain or specimen could not be machined. Consequently, all the cut specimens had to be sanded by coarse and fine sanding, and the total time was 16.2 sec/piece; and (3) the method developed was setting the tool life which was equal to the accumulated machining time performing the cut-surface roughness of 8 µm equivalent to the roughness sanded by using the size grit number of 100. It could eliminate coarse sanding operation. Therefore, the total sanding time remarkably decreased from the existing 16.2 sec/piece to 6.1 sec/piece or 62.2 % reduction of existing time.
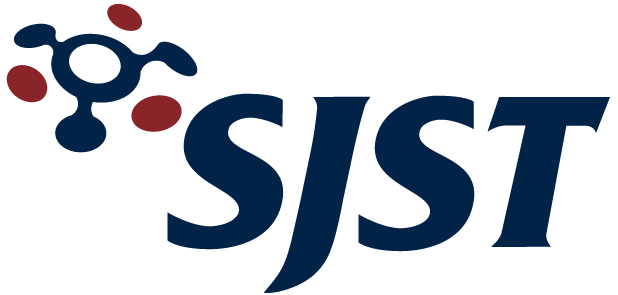