Effects of superheated steam on the drying of rubberwood
Ram Yamsaengsung and Kanokwan Buaphud
pp. 803 - 816
Abstract
Rubberwood drying is the most time and energy consuming step in the processing of wood product. This research studied the effect of superheated steam drying on the drying time required and the physical and mechanical properties of rubberwood after drying. In this study, a cylindrical drying chamber with a length of 1.2 m and a diameter of 0.5 m was constructed and injected with superheated steam. The dimensions of the wood lumber were 1 m × 7.62 cm × 2.54 cm. The wood samples were impinged with alternating cycles of superheated steam and hot air at ratios of 6:1, 4:1 and 1:6 hours until the moisture content was less than 15% dry basis. The conditions inside the chamber were 110ºC and ambient pressure. Continuous superheated steam and continuous hot air were also used for comparisons. The drying rate and the temperature profile for each process were determined.
Initial acceptability of the dried wood was conducted using the prong test and visual inspection. Results showed that if the drying rate was too fast, the dried wood did not pass the prong test due to stress buildup. Therefore, an optimum drying condition was developed based on minimizing defects and reducing
the drying time. For the optimum condition, the following schedule was carried out: (1) saturated steam at 100ºC was used during the first 4 hours of drying to prevent the wood surface from drying too quickly which would minimize the moisture gradient between the center and wood surface, (2) superheated steam at 105ºC and 110ºC was used in alternating cycle with hot air (80ºC) during the main drying stages to rapidly remove the free water and majority of the bound water inside the wood, and (3) hot air was used continuously during
the final stages of drying to reduce the relative humidity inside the chamber making it possible for the removal of the residual bound water. This process successfully reduced the drying time to less than 2 days without causing any defects which compared favorably to the conventional hot air drying process of 7-8 days. Moreover, results of the mechanical properties for the optimum condition showed that the shear-parallel-to-grain was 13.46 MPa and the compression strength parallel-to-grain was 37.73 MPa, both of which were higher than the literature values. Thus, using superheated steam in conjunction with hot air presents a substantial saving in operating time and energy consumption compared to the conventional method while retaining the desired mechanical properties of the wood.
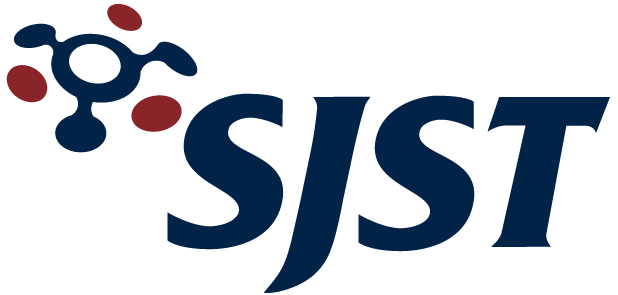